化学産業においては、大量のエネルギー消費とCO2排出量が大きな課題になっている。2050年のカーボンニュートラルは、従来の化学合成プロセスでは実現することが難しいとされており、企業にとってはそれに替わる製造プロセスの導入が急務になってきた。そこで、注目されているのが電化による「有機電解合成」である。この手法を活用すれば、「低エネルギー」「クリーン」さらには「低コスト」を実現することが可能になる。しかし、従来の有機電解合成においては「低生産性」「溶媒抵抗によるエネルギーロス」「支持電解質による廃棄物の発生」などの問題が山積している。それらの課題を一挙に解決できるのが固体高分子電解質(SPE)電解技術であり、その技術を世界に先駆けて研究開発しているのが横浜国立大学 大学院工学研究院の信田 尚毅准教授だ。信田准教授はこのSPE電解技術を社会実装するために、2024年にベンチャー企業も設立している。今回はSPE電解技術の特長や、それが生まれた背景、そして社会実装に向けての今後の取り組みについてお話を伺った。
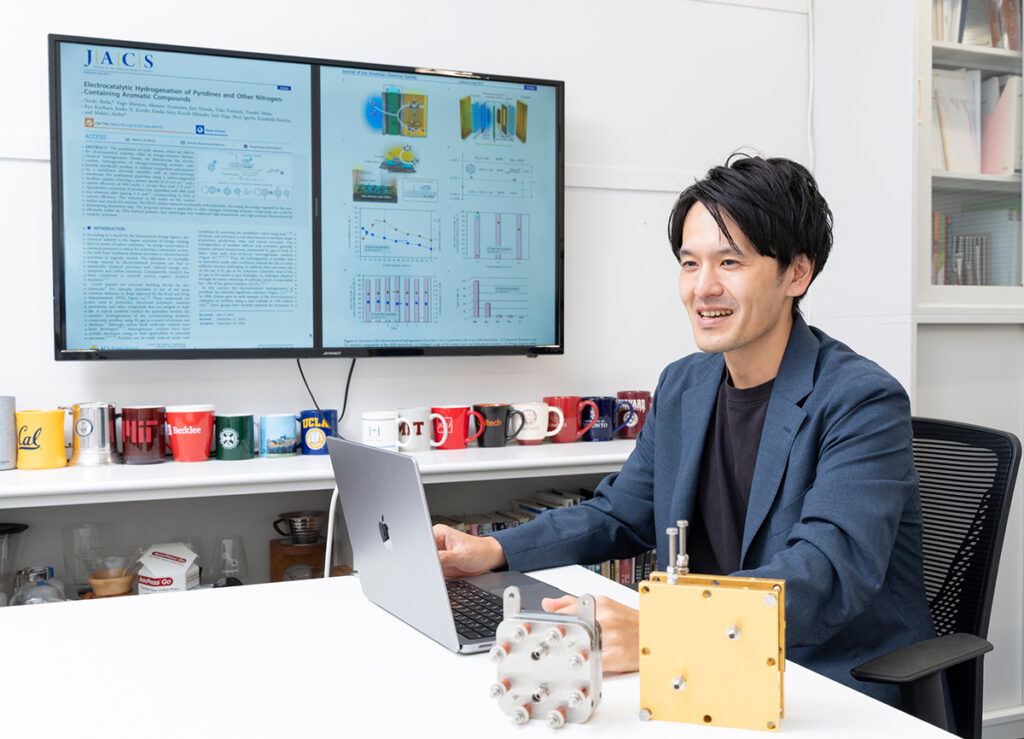
電解合成の3つの課題を解消するSPE電解技術を開発
Q: 現在取り組んでいる研究の概要を教えてください。
研究している技術は「有機電解合成」と呼ばれており、平たくいえば「電気分解」です。通常の電気分解は、水から酸素と水素をつくりますが、これはそれをもっと価値あるものに変える技術になります。
我々はプラスチックや樹脂の原料、医薬品や農薬などの有機物を製造する際に、この電気分解を応用しようと考えています。電気分解による有機物の生成は、化学反応による化学合成と比較すると日が浅く、1800年代ごろに概念が登場しました。それ以降、連綿と研究されてきて、我々もすでにさまざまな手法で有機物の電解合成に取り組み、実現してきました。そして近年になって急激な盛り上がりを見せています。
その理由は、世界的によりクリーンに、サスティナブルにモノづくりをしなければいけないという価値観が大きく共有されてきて、その手段として電気によるモノづくりというトレンドが起こってきたからだと思います。これまで有機物を生成する分野においては、熱をかけて反応させる「化学合成」が中心でした。それがエネルギー効率の向上や環境負荷の低減に重きを置かれるようになり、電気の力による有機合成の考え方が取り入れられるようになりました。
化学産業のCO2排出量は、国際エネルギー機関IEAの調査によると1.37ギガトン。さまざまな産業の中でも、第3位の排出量の多さになります。エネルギー消費になると、全産業の中で第1位に算出されます。このように現状では大量のエネルギーを使ってCO2も排出している状態ですが、これをすぐに止めるとなれば、プラスチックや樹脂が使えなくなり、あらゆる電子機器に大きな影響を及ぼします。その他にも、医薬品や農薬もつくれなくなります。そうなれば、我々の生活は成り立たなくなってしまいます。
なぜ大量のエネルギー消費やCO2排出が起こるのかというと、従来の有機物の生成では100℃以上の高温と、数十気圧の高圧が必要だからです。この条件がなければ、目的の反応が進まなかったり、非常に遅くなったりするためです。今後、よりエネルギー効率の高い製造技術が求められてくるため、我々は、この化学反応による有機物の生成を電気分解に転換することを考えました。 電気分解に置き換えることで、まず再生エネルギーを直接利用することができます。そして、電気分解であれば常温常圧で進められるので、従来の高温高圧による生成プロセスから脱却することが可能になります。
年間何十万トンという巨大なスケールのエンジニアリングを確立しているのは、化学(熱)反応の1つのメリットではあります。しかしその一方で、反応設備をこれから新たに導入するのは高圧高温という制約条件が求められるため、コストや安全面においてもリスクになってきます。そういう時に常温常圧でできるコンパクトな電解反応設備を提供できるのは強みになってくると考えています。
それに加えて、もう1つ強みとなるのは、酸化還元反応という点です。通常の酸化還元反応では、廃棄物(副生成物)が発生します。たとえば、反応に必要な酸化剤・還元剤を生成物と同じ量、もしくはそれ以上使用するのが一般的です。その結果、これらの試薬が分解・変化して、廃棄物(副生成物)を生み出します。これを電解合成(電解反応)にすれば電子をそのまま試薬として活用できるため、廃棄物を生み出さずにクリーンな反応を実現できます。さらに大幅にコストも削減可能です。
化学反応と電解反応での試薬にかかるコストを比較してみると、次のとおりです。例えば、酸化剤では1モル(mol)あたり過マンガン酸カリウムは1,500円、酸化クロムは5,000円。還元剤ではトリメチルアミンボランで1万5000円という概算価格になります。1モル (mol)とは物質量の単位で、原子ごとに重さが異なってきますが、肥料や医薬品、プラスチックなどの化学製品では生産量が非常に多いため、モルのスケールも桁違いに膨大になってきます。当然その分コストにもはね返ってくることになります。また、この試薬は使ったら終わりではなく、廃棄物も出てくるため、そこにもコストがかかります。
これを電解合成にして電子試薬を使えば 、1モルで5円以下という低価格に抑えることができます。一般的な試薬と比べて桁違いの安さです。電気は動力として活用すると高額になりますが、電気を試薬として有機化学反応に利用すれば、非常に安価に抑えられます。 さらに、最初にお伝えしましたが、この電解合成であれば、クリーンで環境負荷も少なく、エネルギー量を大幅に抑えることができます。こうした多くのメリットがあるにも関わらず、実は普及していないのが実態です。
Q: なぜ、普及していないのでしょうか?
電解合成にも3つの課題があるからです。1つ目は、 高温高圧下で行う化学合成に比べて、電解合成は電極反応を基盤とするプロセスです。つまり電極の金属の上でしか反応が起こせないため、二次元の反応になってしまいます。つまり分子が衝突する表面積が小さくなり、液体中で三次元的に分子が衝突する化学合成と比べて、生産性が低くなってしまうのです。2つ目は、有機物を溶解するために有機溶媒が必要なことです。そうなると電極間に溶液抵抗が発生し、電気エネルギーのロス(損失)が起きてしまいます。3つ目は、電気分解を促進するための支持電解質が必要なため、それによる反応の制約が生まれてしまうことです。先ほど化学合成に比べて、電解合成では電子を試薬にできるため廃棄物が少ないと言いましたが、反応自体ではたしかに廃棄物は抑制できます。その一方で電気を流すために、支持電解質とよばれる非常に大量の試薬を溶かす必要があります。化学プロセス(化学合成)では不要な試薬を電解合成では使うため、特別に必要になってくるわけです。こういうプラスαの要素を組み込むことで、そこでできた不要物をリサイクルしたり、廃棄したりする作業が発生します。その結果、 分離精製費や廃棄費用などが全てコストとして載ってきます。
電解合成はメリットもありますが、その反面このようなデメリットも生まれるため、なかなか社会実装できないように思います。そこで私たちは、これらの課題を解決できる電解技術を研究開発しています。それがSPE電解合成(Solid-Polymer Electrolyte/固体高分子電解質)と呼ばれる技術です。SPE電解は数十μmから数百μmの厚さの固体フィルム(固体高分子電解質)のなかをイオンが移動できる仕組みになっています。このSPE電解を用いれば先ほどの3つの課題をすべて解決することが可能です。1つ目は、表面積の小ささです。これは、三次元多孔質とよばれる非常に表面積が大きい電極を用いることで解消できます。2つ目のエネルギー損失については、電極内を数百μmという薄さで組み込むことで、電気抵抗を抑え、エネルギー損失をミニマムにすることができます。3つ目の支持電解質については、SPE電解では固体高分子膜でイオン輸送を担うため、支持電解質が不要になり、廃棄物も大幅に削減することができます。つまり支持電解質フリーで反応ができる技術になっています。
Q: SPE電解技術は、元々あった技術だとお聞きしています。なぜ、その技術を電解合成に使おうと思われたのですか?
おっしゃるように、この技術は我々がゼロからつくり上げた技術ではなく、この装置の構成自体は燃料電池や水電解などでも使われています。なぜ有機物の生成に、この技術を応用したのかというと、政府が目指す2050年のカーボンニュートラルの実現のためです。ある程度開発されてきた技術であれば、ラボからプラントスケールまでの基礎技術の開発期間を大幅に短縮することができます。これだけ聞くと、燃料電池や水電解の技術を流用しているだけに聞こえますが、触媒1つとっても転用することが難しく、有機物に合った新たな技術開発が必要になってきます。
Q: この研究テーマの独自性はどのような点にありますか?
まず、こういった装置の中で有機の電解反応(電解合成)の開発を行っている研究グループがほとんどいないことです。そのため、どのような有機電解反応ができるのかという既存の知見がほとんどありません。我々自身で積極的に新しい例を示していくことが必要になり、我々の有機電解反応のデザインそのものが独自性を持つことになると考えます。
もう1つは触媒の選択です。「触媒」は、目的の反応を行うために非常に大きな役割を果たしており、この触媒の選択も自分たちで行います。専門用語では「電極触媒」と言います。実際には、我々は電極触媒の開発も行っています。どういう元素(素材)を用いて、どういった粒子の大きさに調整し、どういう電子状態のものをつくるかによって、反応が大きく変わってきます。実際、電極触媒をつくり込むのは難易度が高く、相当な技術力が必要になります。
それに加えてもう1つ、この研究の難易度を高めているのは、有機の反応開発という有機化学分野と、電解合成という電気化学分野の両方の知識・経験が必要なことです。有機化学と電気化学は、どちらも化学というワードが使われていますが、専門性が大きく異なるため、両方に精通している研究者や技術者は非常に少ないのが現状です。これは研究の現場でも事業の場面でも大きな課題になってきます。例えば、有機物を熱反応で製造している企業は、電解反応や電気を活用した技術について知見がないために、全く取り組んだことがないというケースが大半です。
一方で、電気技術を中核にして事業を展開している企業は有機反応(合成)にはほとんど取り組んでいません。両分野の境界領域に立っている人材もしくは事業体が実は非常に少なく、我々がパイオニアになっています。
Q: この研究に至るまでの経緯を教えてください。
私たちの研究室では、私はもちろん私の上司にあたる跡部先生も元々有機電解の研究者です。以前は、古典的な電解装置を用いた有機化合物の電極反応を研究していましたが、先ほど紹介したような企業が抱える問題点を解決するために、今につながる研究開発に取り組むようになりました。
ここで使っている技術のベースになっているのは、国プロのSIP(戦略的イノベーション創造プログラム)で取り組んだ、水素ガスを輸送できるようにする水素キャリアの製造技術開発です。具体的には、トルエンに水素を電気化学反応で付加させて液体化することで、水素ガスに比べて500倍以上の水素を一度に運ぶことができます。それを転用すれば、有機物ファインケミカルがつくれるのではないかと考えました。このように水素キャリアの製造開発のSPEの考え方と、有機電解合成の経験を融合し、この研究をスタートしたのです。
Q: 2024年5月にはベンチャー企業も立ち上げられたとお聞きしました。どのような事業を展開されているのでしょうか?
ElectroFluxion(エレクトロフラクション)という会社を、先端技術インキュベーション企業の先端技術共創機構(ATAC)と共同創業しました。「あらゆる化学品づくりをグリーンに電化する」というミッションを掲げ、医薬品や農薬といった有機物を「電解分解」で開発し、化学プロセスをSPE電解合成に置き換えることを目指しています。
実は当社を設立する前から、化学メーカーを中心にお声がけいただいていました。先ほども紹介したように化学メーカーは有機物(製品)を大量に製造するため、全産業中鉄鋼メーカーに次いで多くのCO2を排出しています。そのため、カーボンニュートラルへの意識が非常に高いです。企業によっては、社運をかけて取り組もうとしています。従来のような化学反応(熱)プロセスを電気に置き換えるのは、設備投資も必要ですし、リスクも伴います。しかし、従来の技術改良だけでは2030年までの目標を達成できても、2050年のカーボンネガティブレベルの目標を達成するには限界があります。それを実現するには、抜本的に製造プロセスの転換を行わなければなりません。その1つの選択肢として、電気に置き換えた「電解反応(電解合成)」に興味を示される企業が増えており、今では多くのご相談をいただいています。
なかには資源回収や無機化学に近いような金属の回収など、我々が当初想定していなかった領域のご相談もいただきます。例えば、電気で金属を分離することに、この技術を使いたいといった要望です。従来の方法だと、金属分離に多くのエネルギーを要するため、電解合成を活用することで、分離や再生をより高効率に実現できるのではないかと検討されています。 今は木材資源のバイオマス関係についても、この技術が使えるのではないかと考えています。当初のターゲットは一言で言うとファインケミカルと呼ばれる機能性の化学品だけだったのですが、今ではそこに収まらない領域にも応用できる手応えを感じています。
世界でSPE電解技術のプレゼンスを示していく
Q: 研究課題としてどんなことがありますか?
少し大きな意味での課題であり挑戦になりますが、まずはベンチャー企業を立ち上げた価値を明らかにしていくことです。スケールアップできる可能性をしっかり示していきたいと考えています。大学の研究室での研究範囲だけでは社会実装までつなげるのは簡単ではなく、それを実現するためには、いくつものハードルを乗り越えなければなりません。
実用化に向けては、ベンチャー企業においても、どういう効率で、どれぐらいの期間運転できるのか、そういったデータを実績として積み上げていくことがこれから求められてきます。それを1つひとつクリアして、パイロット版を開発します。それが想定通りあるいは想定以上に動くようになれば、一気に企業への導入が進んでいくと思います。それは大学という単位で研究しているだけでは、全く届かないレベルです。
Q: これからこの研究を目指す学生に対して、伝えたいことはありますか?
今の世の中の若者たちは「タイパ」「コスパ」を重視する傾向があると言われています。でも、この急激な世の中の変化などを考慮すれば、それも当然のことだと思います。先生から言われたことだけをやっている学生よりも、よほど物事を考えて取り組んでいるのではないでしょうか。ただ、幸せの尺度のように世の中には定量化できないことも数多くあります。そういった定量化できないことまで織り込んで自分のやりたいことや、自分の時間の使い方を決められると、より充実した生き方ができると思います。
例えば、給与などは定量化されているため分かりやすいですが、自分がそこにどのぐらいやりがいを感じるかは、給与のようには数値化できません。そういう定量化(数値化)できないこともしっかりと重視して決断できるようになってもらいたい。
また、周囲の声に惑わされないのも大切です。学生によっては「教員がどう思っているのか」「教員が何を期待しているのか」を意識しすぎてしまう人もいます。そうなると、自分が考える「正しさ」や「面白さ」を主張できなくなってしまいます。自分の感性を大切にして研究を行うためにも、教員の意見やアドバイスを参考にするのも重要ですが、それよりも迎合したり、忖度したりせずに、自分の軸を持つことです。それが最終的には大きな仕事につながっていくと思っています。
学生たちには、ミーティングなどでも自分の言葉で語れるようになってもらいたいと考えています。聞いたことのある言葉の組み合わせでは、その人らしさがでてきません。不格好でも自分の言葉で話せる人はユニークな存在になっていきます。自分の経験や感性に基づく自分のアウトプットが非常に大切です。当たり障りのない意見や考えであれば生成AIのChatGPTを使えば、すぐに実現してしまいます。
未来を予測できない時代になって、自分のやったことが将来につながるのか、あるいは無駄足になるのかは事前に推測することはできません。それでもあえてチャレンジしてみるという、ある種の直感(感性)力をぜひ大事にしてほしいと思います。「あの時これを頑張ったから、10年後にこんなフィールドで活躍できるようになった」──このように異なるジャンルを組み合わせることで、唯一の人材になることができます。これも逆算できないからこそ貴重な存在になれるのだと思います。タイパやコスパを意識するだけでは、ありがちなスキルセットになり、突き抜けることができません。だからこそ自身の直感で行動できることが、これからは大事になってきます。
Q: 今後の展望を教えてください。
目標としては大きく2つです。
1つは、電気にしかできない電解反応の事例を増やしていくことです。今は熱反応との比較で、より効率的に開発できることに特化して取り組んでいます。もちろん、その開発においても社会実装に向けて取り組んでいきますが、それだけでなく電気反応本来の特性を活かした取り組みにも今後は挑戦していきたいと考えています。アップヒル反応といわれる電気特有の反応により、さらに不安定なものをつくることができます。こういう事例をもっと増やしていくことで電解プロセスを理解してもらえることにもつながります。それによって電解プロセスを導入することが、ある種必然になっていくと考えています。
もう1つは、世界でこの技術のプレゼンスを示していくことです。電解反応(電解合成)は、まだまだこれからの技術であり、今世界的にも大きく盛り上がっています。これまで日本でもたくさんの先生方が取り組んできました。私はその先生方からバトンを引き継いだ一人として、新たな道を切り拓いていかなければならないとある種の使命を感じています。
そこで、まずは学術的に世界から見て「日本がメッカだ」と言ってもらえるように成果を出していきたいと考えています。社会からも夢のある技術として期待もされています。そういう期待に対して応えていくことが一番の社会貢献になると思います。当然、我々だけですべてのことができるわけではありません。電解質膜開発メーカーや電極の開発メーカー、触媒メーカー、電解装置メーカーなど、電解反応技術の開発にはたくさんの企業が関わっています。さまざまな企業と協業しながら、世界に誇れる製品を世の中に提供し、日本のモノづくりの発展につなげていきたいと考えています。(了)
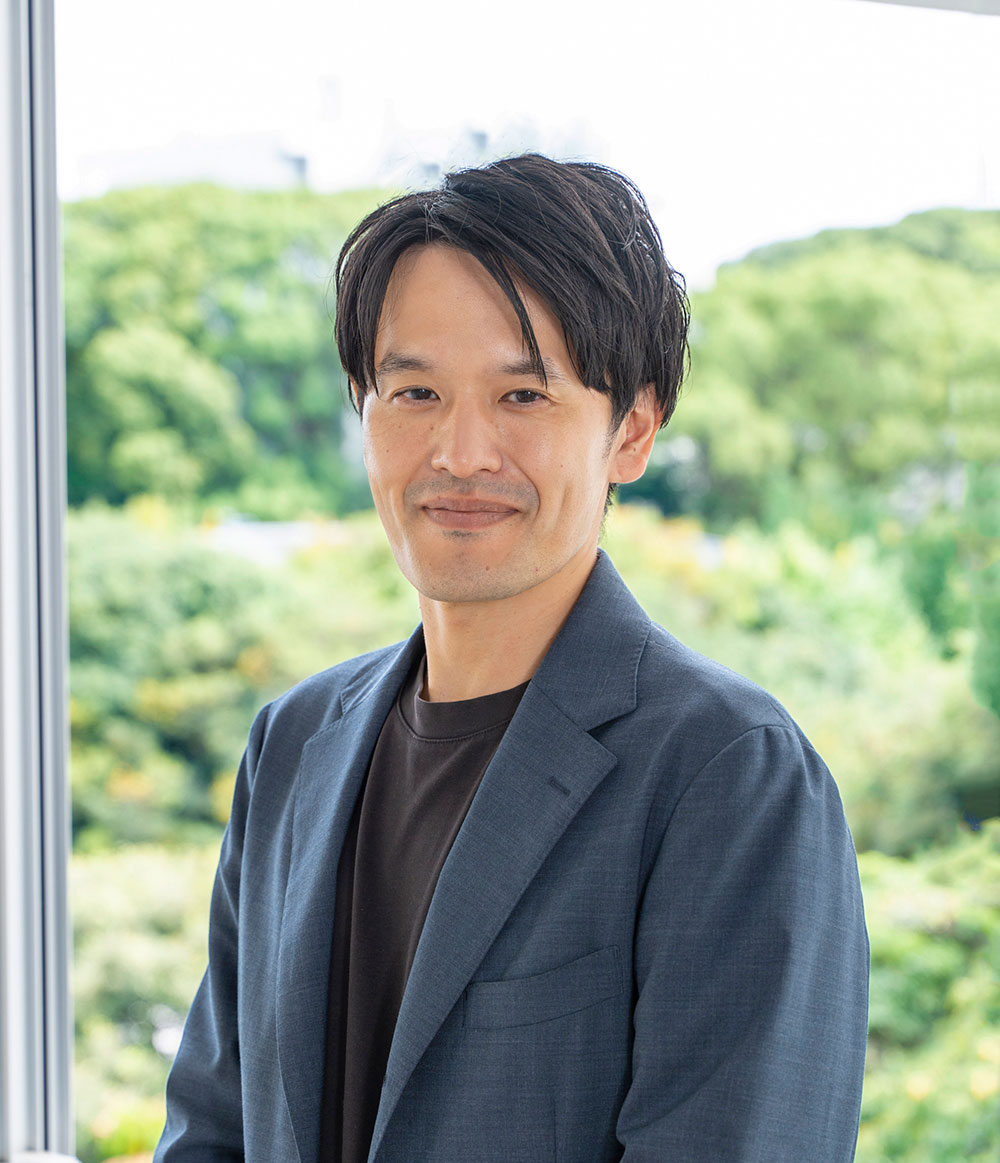
信田 尚毅
(しだ・なおき)
横浜国立大学 大学院工学研究院 准教授
2007年 横浜国立大学 工学部 物質工学科卒業。2013年 東京工業大学 大学院総合理工学研究科 修士課程修了、2016年 同大学 同研究科 博士課程修了。東京農工大学 博士研究員、カリフォルニア工科大学 博士研究員、東京工業大学 特任助教を経て、2024年より現職。2024年には横浜国立大学発ベンチャー称号取得の株式会社ElectroFluxionを創業し、取締役CTOに就任。