「刃物を磨く」ことは奥が深く、一般的には表面に光沢が出た状態を磨いた状態とされているが、真に刃物を磨くためには表面だけではなく「内側」の原子の配列を整えることが重要である。この、内側までが整然と並んだ状態を「超平坦」という独自の用語で定義し、刃物の新たな研磨方法を開発しているのが、名古屋工業大学の江龍修教授だ。江龍教授の技術は、従来磨くのが困難とされていたシリコンカーバイドに実用化され、重電分野のデバイスなどに広く活用されている。「刃物には無限の可能性がある」とし、今後は食物や医療など多分野への展開を視野に入れている江龍教授に話を伺った。
内側の電子配列を整える「超平坦」技術
Q:まずは研究の社会的なニーズについて教えてください。
磨いたものというのは「ピカピカになる」といいますが、そもそもピカピカとは何か、ということを考えてほしいのです。
ピカピカとは、肉眼に対して反射してきた光、または光った光が入ってきて、その見ているものがピカピカに見える状態です。
一方、私が作っているピカピカは、材料の外側にあるピカピカではありません。材料表面の「内側」にある電子達が喜んで動く領域をピカピカにしているのです。
ものを磨くとき、表面を擦ります。擦ると、擦られた内側は原子配列が歪みます。原子の配置が不規則になる、ということですね。原子の配列が歪むと、電子はそこに散乱されて抵抗になり、熱になります。これは、加えた電圧に対してロスしているのですよね。
これに対し、表面はもちろん綺麗で、なおかつその内側、人間の目では見えない内側の原子の配列もまた、綺麗に並んでいる状態。即ち、電子の運動から見て綺麗に並んでいる状態。これを私は「超平坦」と呼んでいます。
超平坦という言葉は、2002年の学会で私が初めて使いました。私の言う超平坦では、人間が溶かして固めたりして一見滑らかに見えるものではなく、内部から原子が配列した状態を、無歪みの状態でまっ平らにすることを指します。
超平坦の例として紹介したいのが、シリコンカーバイドの超平坦化です。シリコンカーバイドの超平坦化によって、デバイスに資する基板を作りました。
シリコンカーバイドはシリコンと炭素が一対一になって結晶状態になっています。結晶構造は非常に複雑ですけれども、基本的なシリコンの周りと同じで正四面体の重心にシリコンがあり、そのシリコンから正四面体の頂点にあるシリコンに向かって4本の手が伸びています。
それと同じで、例えば炭素が真ん中にあったらその周りの4つはシリコンですし、シリコンが真ん中にきたらその周りの4つは炭素です。これらが並んでいるのがシリコンカーバイドですね。
従来、その配列を壊さずに磨くことができませんでした。それを、配列を壊さずに磨けるようにしたのが私の技術で、これが要素技術となります。
シリコンカーバイドが用いられる例として、携帯電話の基地局があります。基地局のスイッチング素子と言われる、シリコンで使われている素子をシリコンカーバイドなどに置き換えることで、半導体デバイスがそのままの場合、5%から3%のロスがなくなるとされています。
さらに、その周辺にあるコイルやコンデンサーなどの素子が小型化できるため、全体でロスをなんと15%も減らすことができます。省エネだけでなくて、うんと小さくできる。例えば冷蔵庫ぐらいのやつが手のひらに乗るくらいになるのですよ。
基地局のように大きい電力を使うところに使えるのであれば、次に目指したいものとして電車があります。エレベーターやクレーンなど大きい電力を必要とするものは、シリコンカーバイドが得意なのです。
シリコンカーバイドは耐熱性が非常に高く、反応性が低いという特徴があります。これは言い換えれば、「磨くのが困難」だということです。
実際に、大阪の地下鉄の御堂筋線に使われました。それが商用として一般人が知るところでは最初だと思います。2010年前後ではないでしょうか。その時は非常に喜びましたね。
その次が東京の地下鉄、そして山手線に使われるようになりました。
Q:現在にいたるまで、どんな経緯がありましたか。
先程「超平坦」という言葉を使いましたが、シリコン自体は平らにして薬品で溶かすことができます。でこぼこでも溶けにくい面と溶けやすい面があるため、ある程度平らにして結晶さえきちんと磨いておけば、薬品で溶かすと平らな面が出ます。
現在は簡単になりましたが、従来はとても難しい方法だとされていました。
シリコンカーバイドはすごく硬くて、ダイヤモンドに次いで硬い材料です。磨くと表面が乱れてしまうのですが、電子が通りやすい方向か通りにくい方向か、お構いなしに磨いていたのです。でもそれを無視して磨くと、壊れて欠けてしまうのですね。
シリコンカーバイドは先ほど申し上げた通り、シリコンと炭素が規則的に並んでいます。加えて、原子が持っている電気陰制度という性質があります。これは、炭素は電子を引っ張りやすく、シリコンは炭素に電子を取られやすい、という性質です。ということは炭素の周りに電子が集まっており、帯電はマイナスです。シリコンはプラスです。
では、そのプラスとマイナスに上手に反応する研磨剤を投入してやれば、マイナスならマイナスの面、プラスならプラスの面がちゃんと出るだろう。これが私のアプローチです。
このアプローチそのものも新しいものでした。やりすぎだ、そこまでやる必要はない、と言われましたね。なぜならば1500度〜1800度の温度にあげれば雑な研磨で壊れた表面が吹っ飛んで、大きな階段状の表面ではあるものの、そこに原子を積んでいけばある程度のデバイスができるだろう、というのが当時の学会・産業界の主張でした。
でも僕は信念がありましたから、プラスとマイナスに上手に反応する研磨剤を作り、フジミインコーポレーテッドという会社と産学共同でものを作りました。作っていく過程も、学会で発表していきました。電子が感じるプラスとマイナスを利用して磨くと、自己組織化的に表面が平らになって、その表面の内側には電子が心地よく走ることを証明しました。
そこに一社だけ、「これは社会的にモノになる」と来ていただいたのがローム社です。ローム社は電子デバイスの企業なのですが、日本で最初にこの原理を使って磨いた、国産初のダイオードを作りました。2005年ごろですね。それから市場に出て、使われるのに5、6年はかかりました。
シリコンとカーボンの原子単位で磨いているぶん、絶対にそれ以上にはなりません。いわば、最終ゴールを最初に決めて取り組んだということです。これが技術の価値化で、私のアプローチといえます。
材料が持つ能力を最大化し、実用化に進める
Q:これから乗り越えていきたい技術的な課題はどんなところにありますか。
原子から見た平坦面、僕が何をやって来たかと言うと、材料がありますよね、材料が持つ能力を最大にして社会に出したいというのが僕の願いです。
今後改良が望まれる材料として、グラフェンというものがあります。
炭素がベンゼン環になり、無限に一層に並んだものをグラフェンと言います。チューブ状になるとナノワイヤーやナノチューブ、カーボンナノチューブと呼ばれるものですね。
グラフェンは、電子の移動という点に関しては非常にすぐれています。地球上で室温だと、最も早いかもしれません。
一層で透き通っており、どこにでも貼ることができます。そのため、抵抗なく電線になったり、タッチパネルの電極にすることもできます。
またダイヤモンド結合に近いため、強度も高いです。うまく編んでいけば、CFRPよりも良い材料ができるとされています。
期待されているこのグラフェンですが、残念ながら現時点では、連続して取り出すことができていません。
いくつか取り出し方はあるのですが、いずれもグラフェンを金属から剥がす工程が必要になります。この「剥がす」工程が難しいのです。
そこで、刃物を使って金属とグラフェンの間に差し込ませ、連続的に作りながら剥がしていく方法が有効となります。
この点について、刃物をどう使っていくのかというのかが私の現在の研究課題です。良いグラフェンをどう作り、どう剥がして、人が使えるようにするか。これが大きなターゲットの一つです。
僕がもう一つ目指したいのは、人が笑顔に普通に暮らすことです。そのためには食べるものがすべて健康で、食べることで健康になることが必要です。
さて、野菜を切るときに使う包丁ですが、その先端はギザギザしています。家庭では包丁を砥石で研ぐため、どうしてもギザギザになってしまうのです。これは、分子がバラバラになっていることを意味します。
分子がバラバラになった包丁で野菜の断面を切ると、野菜の細胞が潰れ、水が出てきたり金属と接触したりして、その細胞がショック死し栄養が壊れてしまいます。
同様の例が、ジューサーの刃です。ジューサーでは、ビタミンを壊しながら回しているため、栄養のロスが大きくなっています。そこで、家庭用の刃物を新しい技術によって磨くことが重要なのです。野菜を切ったとき、細胞は切られた事も分からないぐらいにスパッと切ることができたら、栄養も保たれるでしょう。
食品以外の例を挙げれば、植物を接ぎ木する際にも百発百中接ぎ木できるでしょう。
医療機器等にも応用できると考えられます。ある医療には心臓のこの細胞に対して、本当はこういう材料で切りたいけれども、ないから結局病気が治らない、などの課題が解決できるようになります。
これまで、磨きにくいと呼ばれていた材料も、この原理原則で磨くことができるようになっていきます。刃先には、それだけ可能性があるのです。
私の加工技術では、内側を歪ませずに表面から原子を剥ぎ取っているだけですから、刃先が非常に長持ちします。金属の刃物にしても、2倍以上長持ちになります。そこが従来の考え方とはまるで違う点です。
とがらせたら早くすり減るだろう、欠けるだろうと思われがちなのですが、まったく違います。本当に内側からしっかりと電子が心地よく原子をつないだら、離れないのです。
研究室で開発した、パン切り包丁
Q:この分野を志す学生には、どんな力が必要ですか。
私自身、物理工学専攻というところにはいるのですが、機構長という立場でいますので、大学全体、工学部全体に向けてお伝えします。
私自身も分野が広く、化学から機械から、すべてに関わってきました。そういう意味では特定の分野はありません。VR やARなどの仮想現実の時代も到来します。だけど、実際のもので世界の人たちとやり取りをする夢はやはり大事だなと思います。
例えば包丁1本にしても、本当に「切れる」包丁は今まで世の中にありませんでした。いま研究室にあるパン切り包丁は、世界にたった2本しかない、本当に「切れる」包丁です。
学生には、今あるものを鵜呑みにしないでもっともっと良くなるはずだ、社会はもっと笑顔になるはずだということを真剣に考えてほしいですね。一人ではなくて友達同士、仲間同士をどんどん増やすべきです。
挑戦することは誰でもできます。一歩踏み出す、一歩踏み出そうよ、そのためにはでも自分の専門を調べ尽くし知り尽くさないと他の分野との融合はかないません。だからもっと勉強しよう、ということだと思います。
Q:最後に、今後の目標について教えてください。
まずは研究室で開発した、パン切り包丁を世の中にリリースしたいですね。量産に持っていくとなると、包丁の素材から考えていかなければいけません。一丁3000円の従来の包丁を磨いても、寿命などに限界があります。一丁10万円ぐらいのものにしなければいけません。
日本の良い包丁は世界が買いますから、世界中の人たちを、「切れるっていうのはこういうことか」「切れる物理ってこういうことか」とうならせたい。
そして包丁や食の分野からスタートして、「切る」という概念そのものを変えていきたいですね。ものづくり全体に、「切る」ことの可能性を波及させていきたいです。(了)
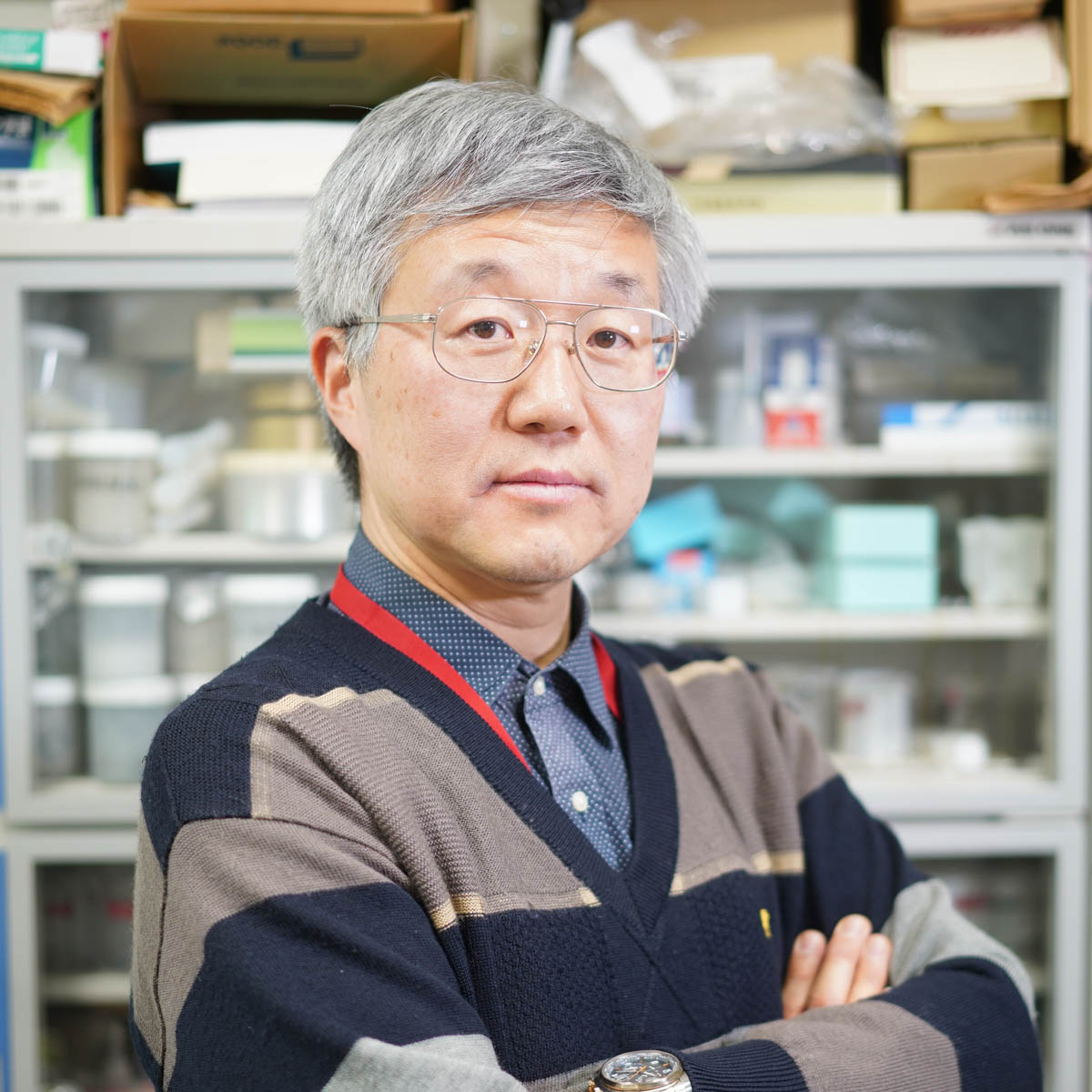
江龍 修
えりゅう・おさむ
名古屋工業大学教授・副学長。
1985年、筑波大学第三学群基礎工学類 卒業。1990年、筑波大学工学研究科物質工学博士課程 修了。博士(工学)。
1990年より筑波大学物質工学系 助手を務めたのち、1993年より名古屋工業大学工学部講師。
1998年より名古屋工業大学工学部助教授となり、2005年より同教授に。
また、2012年より名古屋工業大学副学長も務める。