素材を削り、必要な形状・寸法に加工する工作機械は、長年我が国が世界のトップレベルに君臨しつづける分野だ。こうした技術や知見は日々複雑化・高精度化が進んでおり、職人技などの属人的なものから、加工支援ソフトウェアの開発・普及を通じて一般化されることが求められている。「基盤となる工作機械とそれを使いこなす加工技術、その両方があわさることが必要だ」とし、その両面から実用的な研究を進めるのが東京農工大学の中本准教授だ。今回は世界における日本の製造業の立ち位置やその特殊性、ソフトウェアの必要性についてお伺いした。
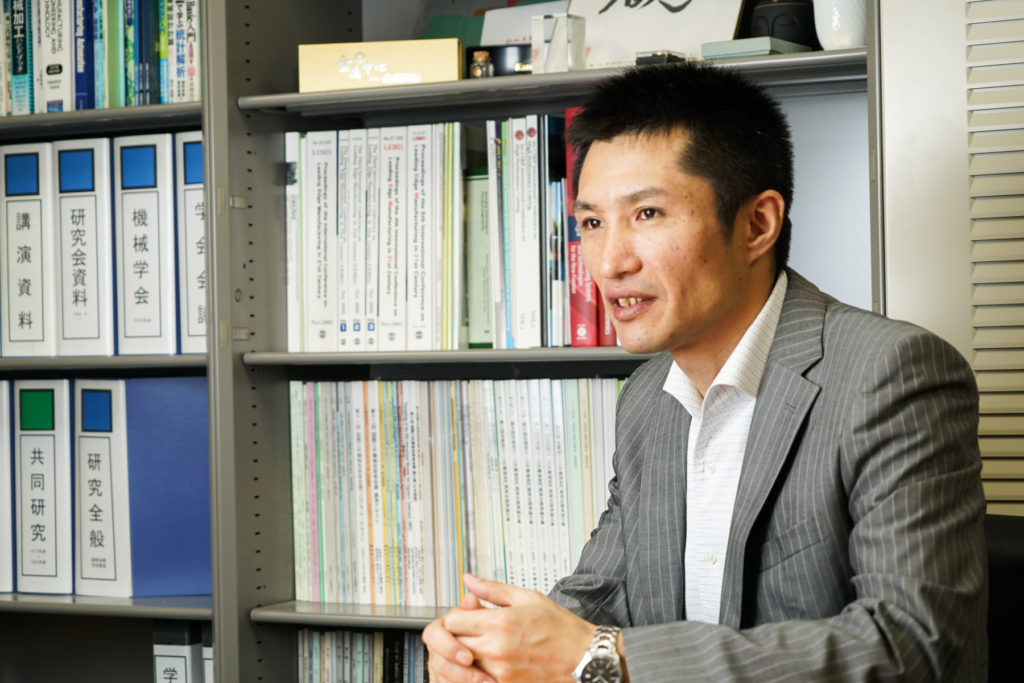
工作機械を使いこなすノウハウをソフトウェア化
Q:まず、研究の概要やニーズからお聞かせください。
研究内容をお話しする前に、まず工作機械についてご紹介します。
穴を開けるためのドリル加工が最も分かりやすい例だと思いますが、何かの素材を削って必要な形状・寸法に加工する機械のことを工作機械といいます。
一般に、工作機械で金属などを削って部品を加工してそれを組み合わせて製品は作られます。またペットボトルやプラモデルなどを作る際に樹脂を流し込むための金型も工作機械で加工しています。 機械を作るための機械であり、工作機械の精度が良ければ最終的な製品の精度も良くなりますから、製造業の基盤をなすマザーマシン、あるいは母なる機械と言われています。
一般の方にはあまり知られていませんが、工作機械は日本が長い期間に渡って世界のトップレベルに君臨している珍しい機械です。ものづくり大国日本の製造業を支えていて、世界のトップメーカーも日本にあります。
日本でよくターゲットとして加工しているものは自動車や家電部品、金型で、最近は航空機や医療用部品の加工も盛んになり、あらゆる分野のものづくりを支えています。
工作機械の歴史は、古代エジプト時代まで遡ることができます。
その後、近代的な工作機械はイギリスで誕生しました。社会科で学ぶ歴史では産業革命の端緒は一般にジェームス・ワットによる蒸気機関の発明とされていますが、蒸気機関の普及には1770年代に開発されたウィルキンソンの中ぐり盤という工作機械が大きな貢献を果たしました。具体的には、この工作機械で加工できるようになった精度の高いシリンダにより蒸気機関の効率が飛躍的に向上したと言われています。
さらに、欧米各国で現在にも通じる各種の工作機械が開発され、自動車の大量生産に伴ってアメリカが工作機械産業の中心となった時代もありましたが、近年では日本とドイツが技術レベルで世界のトップの座を争っています。
生産額としては最近まで日本が世界一だったのですが、いわゆるリーマン・ショックの際に中国に抜かれてしまいました。これが一種のターニングポイントだったわけですが、技術レベルとしてはまだ日本の方が優位な状況です。いずれにしても、日本が四半世紀にも渡って生産額世界一を維持した産業はおそらく他にはないと思います。
一方、日本の工作機械産業の弱みとしては、他産業と同様に人件費や電気、土地などインフラのコストが高い点が挙げられます。また、工作機械を動かすための加工支援ソフトウェアが欧米諸国に依存していることも大きな問題です。さらに、日本の特殊事情として貿易管理令という法律で最先端の工作機械を自由に輸出しても良い国が限られることが挙げられます。世界トップレベルに精度の高い何でも加工できる日本の工作機械を使って、日本の平和を脅かすものを作られてしまう可能性もあるからです。
例えば、いま日本メーカーの高機能な工作機械は、移動させた際の振動を感知して電源が落ち、メーカーのエンジニアが来るまで復旧できない仕組みになっています。これは大変面倒な仕組みですが、工作機械メーカーがユーザーに売った後で盗難にあったり、どこかの国に転売されたりすると、メーカーも責任が問われる可能性があるためです。
Q:そのなかで、中本様ご自身の研究はなんですか?
工作機械を使いこなすノウハウを明らかにしてどのように一般化するか、ソフトウェア化するかという課題について主に研究しています。最近の工作機械は複雑な構造をしていて様々な動きができる、非常に高速で高精度なロボットですから、動かすためにはどうしてもプログラムが必要です。人間が手作業で動かすわけにはいかずプログラムが必須です。このプログラムを作るソフトウェアをcomputer aided manufacturing、略してCAMと言います。
欲しい形状や精度などの情報に従って、工作機械にどのような工具を取り付けて、どんなスピードでどのように動かして削ればいいかを教えてくれるソフトウェアになります。
しかし、先ほどお話しした通り、ハードウェアである工作機械がこれだけ強い反面、日本はこのCAMと呼ばれる加工支援ソフトウェアが非常に弱いと言えます。もともと国産のCAMもありましたが、機械製品や部品を設計するCADと呼ばれるソフトウェアで欧米製が広まるにつれ、徐々にシェアが低下していきました。
この CAMの現状は日本にとって大変残念で、工作機械を使うために絶対に欠かせないソフトウェアを欧米に握られてしまい、工作機械産業の大きな収益源をひとつ失っています。また、将来的に工作機械のIoT化が進んだとき集約された種々の情報を工作機械の動作へとフィードバックする手段が限られる可能性もあります。
工作機械を自動車で例えるとCAMはカーナビのようなものです。カーナビでは、行き先と、高速道路と一般道路のどちらを優先するかなどドライバーの好みを入力すれば行き方を教えてくれます。しかし、カーナビもまだまだ賢いとは言えません。自動車は今のところ有人運転が前提で、細かなことは人間が判断すれば良いからです。
人間は「700メートル先を左折です」とカーナビに言われたら一番左の車線に入っておこうとしますし、バスが一時停止していれば一旦別の車線に移るなど、周りの環境に応じて適切に対応します。一方、工作機械は基本的に自動運転が前提ですからCAMは現時点でももっと高いレベルが必要なのに、十分な機能はまだ備わっていません。
結局、高度な加工をしようと思えば、ベテランの方がコンピュータの前で一生懸命にそのノウハウをCAMに入力してプログラムを作り、間違いがないかテスト加工して試行錯誤しなければいけないのが実情です。
昨今の人工知能ブームもあって自動車の知能化が注目されていますが、将来的には人工知能が進化してカーナビ機能を組み込んだ自動車自身が自律的に運転するようになるかもしれません。工作機械も同様に、CAMの機能が不十分でも工作機械自身が考えて対処できれば良いのですが、そのためには今より格段に賢くなる必要があります.そこで、ソフトウェアであるCAMの高度化とともに、ハードウェアである工作機械の自律化についても取り組んでいます。
さらに、それらで開発した技術を基に1mm以下の実寸大の雪の結晶など、マイクロ、ナノメートルスケールの非常に微細な形状の精密な加工にも挑戦しています。実用的な加工例としては、DVDのピックアップレンズなど光学的な用途のものが多いですが、最近ニーズが高まっているものとしては、自動車のヘッドライトで使われる反射板の金型などがあり、非常に小さい溝がA4サイズの曲面上に無数にある複雑で微細な形状をしています。プログラム上の指令は1ナノメートル、1000分の1ミリの更に1000分の1の刻みになって膨大なデータ量となり、CAMを使わないと人手でプログラムを作ることは不可能です。
学生にとって工作機械は馴染みがなく地味ですが、精度は非常に高いといえます。一方、人間の腕のような形をしている産業用ロボットは派手ですが、精度はそれほど高くありません。
余談ですが、機械の運動に関する精度は「繰り返し位置決め精度」と「絶対位置決め精度」の2種類に分けられます。
繰り返し位置決め精度は命令したらどれだけ同じ位置に繰り返して行けるかという指標になります。これは産業用ロボットでもそんなに悪くなく、プラスマイナス数十ミクロンくらいの精度です。一方、工作機械は繰り返し位置決め精度も当然必要ですが、それに加えて絶対位置決め精度も必要で、これは産業用ロボットが苦手にしているものです。
もう少し説明すると、繰り返し位置決め精度は、命令した(x,y,z)=(10,10,10)という位置でも違う位置でも、とにかく同じ位置に行けばいい訳です。しかし、工作機械では必要としている形状や寸法の部品を生み出すために、同じ位置に何度も行くだけではなく、(10,10,10)と言われたら必ずその場所に行く必要があり、それができなければ高い精度の加工ができません。つまり、工作機械は繰り返し位置決め精度も絶対位置決め精度も共に求められる高度な機械、ロボットということになります。
Q:開発と普及、その両方を担っているということなのですね。
そうですね。製造業が今後も発展するには基盤となる工作機械とそれを使いこなす加工技術を絶対に誰かが研究しないといけません。実際にこの分野はどの大学にも存在すると思いますが、少し歴史が長いため時代遅れに感じる人もいると思います。大学の研究者がさらに増えることを期待していますが、工作機械は既に産業として成り立っていますから、何をいまさら大学で研究するのかと言われることもあります。
そこで必要性を説明するために、システムキッチンを例として思い浮かべてもらっています。つまり、工作機械で何かを加工することを、キッチンで何かを調理することに当てはめたとき、同じキッチンと道具があって同じ材料があれば、誰もが同じ料理を作ることができますか、と尋ねると答えはNoだと思います。キッチンや道具の使い方、材料の選び方や調理の仕方が総合されて美味しい料理となるはずです。また、キッチンや道具も進化しますし、新しい材料もどんどん出てくるわけですから、新しい調理技術も不可欠です。それは誰かが研究してレシピを公開しないと、全て自分で試さないといけなくなります。
工作機械や加工技術も同様で、すでに商品化されて強い分野だからといって研究しなくてもいいというわけではないのです。世界的な流れとしても、ドイツが提唱しているIndustry4.0を代表に、生産設備に様々なセンサーを取り付けて情報を集め、人工知能を駆使して製造業をデジタル化して革新しようという動きが各国にあります。
また、大量生産と同等のコストで、個別にカスタマイズされた製品を生産するMass-Customizationが近年の製造業のキーワードになっています。Mass-Customizationは製造業の究極の目標であり、人件費やインフラのコストが高い日本でものづくりを続けるためには、他国よりも積極的に推進する努力が必要になります。
いま世界中で最先端の工作機械を手に入れることはできます。もちろんCAMも市販されています。そうすると様々なコストが高い日本は不利になり、ものづくりの現場が日本から失われてしまうことが心配です。
新興国から技術的にも追い上げられていますが、まだ日本の現場はかろうじて生き残っています。この要因は、加工の仕方に関するノウハウの蓄積とそれを体得しているベテランと呼ばれる現場の熟練者の存在です。しかし、ベテランもリタイアを迎えて年々減少していきますし、一刻も早く競争力を確保、維持する取組みが必要という危機感が研究のモチベーションです。工作機械を使いこなすノウハウをソフトウェアに落とし込んで共有するだけではなく、新しい工作機械や工具、材料などに対しても適応させることが重要だと思います。
我々の分野では、熟練者のノウハウや属人的な能力などの暗黙知を「技能」と呼び、これを誰もが使えるように一般化した形式知を「技術」と呼びます。技能を技術化すると世間に広まってしまうため、誰もが同じことができようになって競争力を失ってしまうことも危惧されます。そのため会社独自のノウハウを生かしながら、要所は社内に留めて他社と差別化できるようにソフトウェアの開発でも配慮しています。
Q:属人的だったものを誰でも理解できるように記述し一般化して、その会社で閉じてしまう。社員は誰でも身につけられるけれども社外には出さないのが一番いいですよね。
その仕組み自体はどの会社にも適用できると考えています。先ほどから加工の仕方と言っていますが、我々の分野ではこれを工程設計と呼んでいます。加工の工程を設計する、ということで工程設計です。 どこをどの工具でどういう順番でどのように加工するのかを熟練者が考えて、工程設計の結果をCAMに入力して工作機械を動かすためのプログラムを作るのが加工までの流れです。
少し前まで二次元の図面を見て、三次元形状を想像しながら熟練者がこのように加工したら良いのではないかと考えていました。
今では、CADというソフトウェアで三次元のモデルが作れるため、熟練者のノウハウを織り込んで自動で工程設計するシステムを開発したいと考えています。つまり目標とするモデルを入力すれば、こういう形状だとここはこう加工しましょう、それは何番目にしましょう、ということを提案してくれる工程設計支援システムです。
現状では、使用する工作機械や工具、加工する形状を限定することなく工程設計を施して、CAMへその結果を自動で入力するのが目標です。ただ、工程設計は完全自動にするよりも工程の候補をいくつか上げて最終的に人間が決めるようにしようと思っています。そこで、候補の中から最終的に選択する際に企業の伝統や熟練者の好みを反映させる余地を残した、電車の乗換案内のような仕組みを提案しています。工作機械では素材から目標の形状まで削り取りながら加工しますが、その過程に対してどういう工程を設計するかで、加工精度や時間や工具のコスト、消費電力などが変わります。
工程設計に関わる従来の研究は、これが最適だと候補を一つに絞ってしまう例が多かったのですが、その“最適”は評価する人や状況によって様々です。電車の乗換案内でどれを選ぶかが人によって違うように、この工程が最適と言われても人によっては納得できず、同じ人でも状況に応じて判断が変わるはずです。
例えば、納期が近ければ時間が最優先になりますし、余裕があれば時間かけて安い工具を使って削ることを望む場合もあります。そのため、工程設計の候補をいくつか提示して実際に工作機械を使用する人にその都度選んでもらう仕組みにしようとしています。
研究成果がすぐに反映される魅力
Q:これまでのご経歴をお話しください。
高校を卒業して大阪大学に入学して以来、博士の学位を取得するまで約9年間在籍しました。
もともと研究者志望ではなく、大学院生のときには就職活動もして、ある企業から内定を頂いていました。でも、同期になる人達と実際に会ったときに周りがとても優秀で場違いに感じ、ちょうど指導教員の先生に誘われていたのもあって勉強する時間稼ぎのつもりで博士課程に進みました。当初、博士の学位を取った後は企業への就職も考えていましたが、博士課程での研究生活の自由さに慣れてしまい、企業に就職すると好き勝手できない気がして、研究者として大学に残りました。
2種類の研究者が世の中にはいると思っています。生き様が研究者のタイプと職業が研究者のタイプで、私はおそらく後者です。ずっと考え抜いて徹夜するみたいなことは好きではないし、同じ分野の先生方や企業の方からの評価が得られなければその研究はすぐに止めてしまいます。大学の研究者としては、ちょっとダメかもしれません。 論文を書かないと研究者としては評価されませんから、学術的な論文も書きますが、それよりも産業界で既にニーズがあって必要とされている技術の開発が楽しいと感じています。
Q:大阪大から最初に就職されたのはどこですか?
神戸大学です。4年間お世話になって、研究室の教授の先生がご退職されたため大阪大学に異動しました。同じ大学ではありましたけど、学生時代とは違う専攻の研究室でした。大阪大学の研究室でも、また教授の先生が4年目でご退職され、次のポストを探していたときに現職の募集があり、2012年から東京農工大学でお世話になっています。
規模の大きい国立大学だと研究室に教授がいてそのスタッフとして准教授などがいますが、東京農工大学は少し変わっていて、若い准教授でも一つの研究室を独立して運営できる仕組みになっています。若手の教員を育成するテニュアトラック制を徹底しているため、恵まれた環境が用意されており、非常に楽しく研究させてもらっていますし、様々な分野で集まってきた優秀な方々から刺激を受けることも多いです。
また、今の研究室には16人の学生が所属していますが、教員一人でこれほど多くの学生を指導できる国立大学はほとんどないと思います。多くのテーマに手広く取り組め、共同研究も気軽にできることは大きなメリットだと思います。
Q:課題として感じることは、どんなことでしょうか。
実は、我々の工作機械や機械加工の分野は産業界と極めて密接な関係にあるため非常に恵まれていると思っています。他分野と比べて学会にも企業の方が相当な割合で構成員として参加されています。共同研究も非常に活発な分野ですし、大学で生まれた技術が共同研究を通じてブラッシュアップされ、すぐに商品化されることもあります。
工作機械業界が世界的にトップレベルとは言っても、日本の工作機械メーカーの規模はそれほど大きくありません。最大でも従業員数千人程度で、オーナー企業が多いこともあり、皆さんフットワークは軽いと思います。また、日本工作機械工業会という工作機械関連の業界団体では、定期的に大学の研究者との交流会を開催しており、産業界と学術界の間に壁がないのは非常に良いことだと思います。
全般的な課題や不満としては、成熟した産業、あるいは確立した技術と世間で思われている面もあって、大型研究費などで政府や関連団体からのサポートがあまりないのはつらいところです。ただ、客観的に見れば、共同研究がやりやすく企業から研究費を得やすいため、仕方ない面はあるのかもしれません。
Q:学生さんはいまいらっしゃいますか?
現在、学部生と大学院生を合わせて16人学生がいます。研究室に正式に所属するのは学部4年生からで、8割程度は大学院に進学します。最近の工学部のトレンドとして大学卒業後は大学院で修士号まで取得するものと考えている親御さんが多く、大学入学時に大学院へ進学するつもりの学生も多いです。
さらに進学して博士の学位まで取得する学生もいます。我々の分野では大学や研究機関だけでなく民間企業へ就職する学生も多く、いわゆるポスドク問題はほとんど存在しませんから、経済的な問題を除けば気兼ねなく進学しています。
Q:企業と積極的に研究なさっているということで、今後こういう企業と一緒にやっていきたいというところはありますか?
共同研究はいくつか経験していますが、工作機械メーカー、ユーザー問わず、加工技術に関わる幅広い分野の企業と一緒に共同研究できればと考えています。まだ経験のない企業の方には、大学側は共同研究に前向きで敷居は高くない、ということを知ってもらいたいと思います。
例えばエンジニアを一人雇えば、各種保険料も含め相当な金額が必要だと思います。それに比べれば割安で、企業側は大学の教員と学生に何かを考えさせてアウトプットを得ることができます。コスト面から考えればメリットは大きいですし、気軽に始めてもらえたいと思います。ただ、成果を大きく左右する学生は毎年入れ替わるため、あまり成果が出ない可能性も有りますので、過剰な期待はしないで頂けると助かります。いずれにしても、共同研究は大学側が最先端のニーズを知る良い機会ですから基本的に大歓迎です。
また、共同研究は学生のモチベーション向上にも繋がります。実際に困っている人に求められて何かを研究するのと、教員に言われたから仕方なくやるというのでは学生のモチベーションが全く違います。
誰かの役に立つことや、この問題が解決できればいくら儲かるという具体的な話を企業の方から直接聞くことが大事だと思っています。例えば基礎科学などの研究分野は、自分の開発した技術が20年後か30年後に使われるかもしれないし、使われないかも分からない面があります。波及効果の大きい長期的な視点からの研究は大学の担う重要な役割ですが、自分たちが研究した成果がすぐに現場で使われることにやりがいを感じる人も多いと思います。
そういう意味では、他分野とは少し違った楽しさを感じることができる、魅力的な分野なのではないでしょうか。(了)
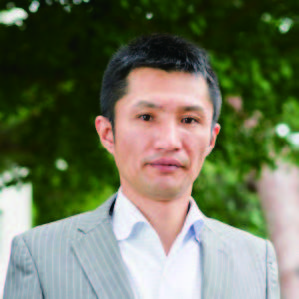
中本 圭一
なかもと・けいいち
東京農工大学大学院 工学研究院 准教授。
1999年、大阪大学工学部 生産加工工学科卒業。同大学院工学研究科生産科学専攻博士課程 修了後、2004年から2007年まで神戸大学 工学部 機械工学科 助手。2007年より神戸大学大学院 工学研究科機械工学専攻 助教となり、2008年より大阪大学大学院 工学研究科 機械工学専攻 助教、2011年より同講師。2012年より現職となる、2016年にテニュア取得後現在に至る。